Which Is Better? — Screw Compressor VS Piston Compressor
In the air compressor market, screw air compressors and piston air compressors are the leading contenders. Professionals often utilize this comparison to highlight the advantages of each model.
Piston air compressors were among the first to enter the market, gaining significant popularity early on. However, screw air compressors were introduced later and have since added a high level of operational intelligence.
A clear trend is observable, where piston air compressors are gradually replaced by screw air compressors, a change that is ongoing. Predictions suggest that screw air compressors will find wider applications in industrial production soon, resulting in a continuous rise in their market share.
When faced with the decision between a rotary screw air compressor and a piston compressor, it is essential to understand their similarities and differences for optimal equipment performance.
Compressors are vital in the daily operations of many businesses, with strong demand across various gas sectors. Both compressor types are in use, but air compression dominates the applications. Currently, stationary screw air compressors hold around 40% of the air compression market share, while piston air compressors account for approximately 21% (measured in US dollars).
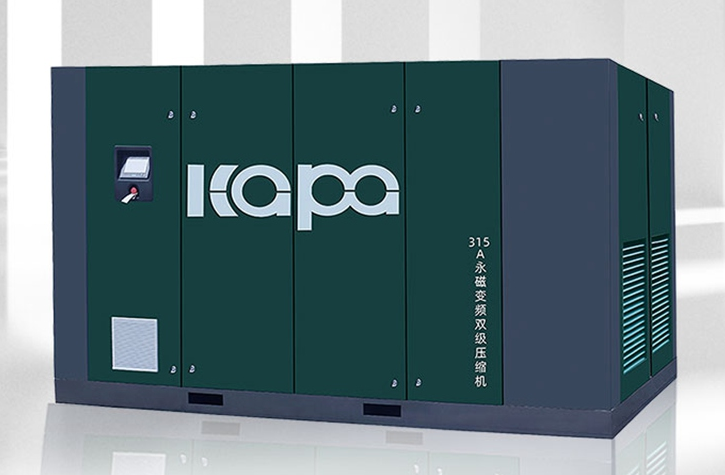
What Sets Rotary and Piston Compressors Apart?
Structural Differences
The screw air compressor comprises several components, including the oil screw main engine, electric motor, oil and gas separator, oil pipeline system, cooling system, gas pipeline system, and electrical control system. Meanwhile, the piston compressor consists of the main compressor unit, cooling system, regulating system, lubrication system, safety valve, electric motor, and control equipment.
Distinct Features
Screw air compressors are favored for their low vibration, non-requirement of anchor bolts for foundation support, low motor power consumption, minimal operational noise, high efficiency, stable exhaust, and absence of wearing parts. The compressed gas from piston compressors typically does not contain oil, negating the requirement for a degreasing device. Nonetheless, piston compressors have downsides including higher motor power consumption, unstable exhaust pressure, elevated exhaust temperatures, increased noise levels, and higher maintenance demands.
Failure Types
Screw air compressors usually experience few failures and require minimal routine maintenance like air filter, oil filter, and oil-gas separator replacements. In contrast, piston air compressors face particular challenges such as incomplete oil scraping, inadequate sealing, and high exhaust temperatures, often causing oil to enter the compressed gas.
Which Is Better: Rotary or Piston Compressor?
Performance Analysis
Reliability: Piston air compressors are less reliable due to their many components and susceptibility to wear, leading to high maintenance needs. Overhaul intervals are generally around 8,000 hours. In contrast, screw air compressors offer high reliability with fewer components that do not wear out easily, requiring minimal maintenance, and have overhaul intervals between 40,000 to 80,000 hours.
Dynamic Balance:
Piston compressors can generate significant vibrations due to unbalanced forces, often needing foundation support. Conversely, screw compressors maintain stability during high-speed operation without needing a foundation.
Pressure Consistency:
Piston compressors often suffer from fluctuating exhaust, requiring large-capacity air tanks. On the other hand, rotary screw air compressors provide uniform and stable pressure without generating substantial pulsations, negating the need for oversized tanks.
Air Quality:
Piston compressors produce lower quality air with higher exhaust oil content, increasing post-processing costs. Screw compressors, however, achieve excellent air quality with low exhaust oil content, minimizing additional processing expenses.
Price Comparison
Piston air compressors are generally more affordable due to their less complex production requirements, while screw air compressors entail more advanced technologies, resulting in higher costs.
Stress and Capacity Adaptability:
Piston compressors can operate efficiently over a broad pressure range, while oil-injected screw compressors are limited in high-pressure applications.
Operation and Maintenance:
Piston compressors require active supervision and lower automation, while screw compressors can be automated, allowing for unattended operation.
Conclusion
Piston air compressors are a cost-effective choice, reducing production and maintenance costs. However, considering the growing demand for reliability and efficiency, the shift towards high-efficiency screw compressors is gaining momentum, enhancing air compressor stations’ overall performance.